Gearheads are sometimes called “epicycloidal” gearheads because the points on the rotating planets trace epicycloidal curves as they turn. The term “planetary” is also applicable because the rotating action of the entire assembly about the central sun gear mimics the movement of a solar system. Planetary gear trains are being used increasingly as actuators in applications where more torque is required from a smaller drive train package. Planetary gear trains are also used for differential systems and applications where very low reduction ratios are required. The input, output and auxiliary shafts can be connected to any of the three stages to achieve the speed/torque requirements of the application.
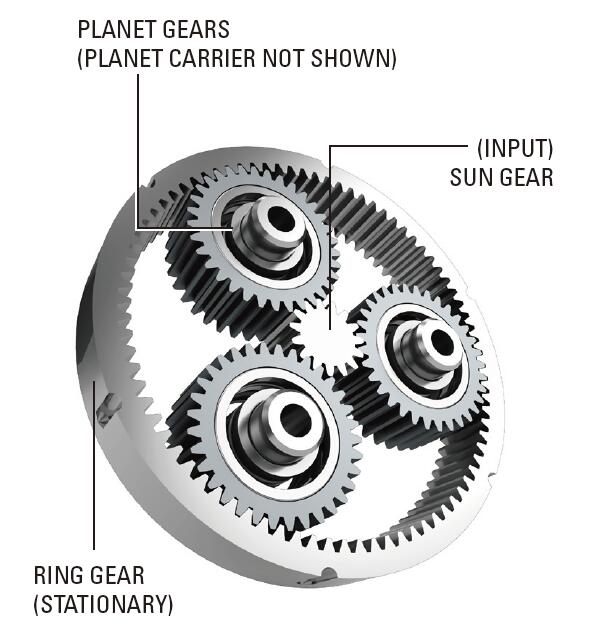
Main components of a typical planetary geartrain
Construction of a Typical Planetary Gearhead
A planetary gearhead is comprised of a sun gear, a ring gear, and a planet carrier assembly that uses three to five planet gears. The sun gear is generally the motor pinion, and the ring gear is generally in the housing. The planet carrier is usually a stamped or cast plate with a number of studs attached on which the planets revolve. The planet gears share the load, revolving around the sun gear. The output shaft is generally attached to the planet carrier of the output stage. Lubrication is usually a thick, sticky grease.
Calculating Planetary Gear Ratio
In most planetary gear motors the sun gear is the input, the planet carrier is the output, and the ring gear is kept stationary. However the sun, carrier and ring can be the input, the output or can be held stationary. Which piece rotates determines the gear ratio and whether the gear set is a speed reducer or an increaser in which direction the output turns.
Advantages of Planetary Gearheads
Compact size and lower weight: as much as 50% reduction in diameter with same torque output as an equivalent parallel shaft gearhead.
- High torque density
- Several planets share the load rather than one gear, the more planets the more load sharing.
- Longer gear life at similar loads.
- Lower backlash than equivalent parallel shaft gearheads.
- High efficiency. 97% per stage is common.
- Typical ratio per stage is 9:1, 4 stages up to 9000:1.
- Coaxial center shaft arrangement, no offset output shaft, easy to install.
- Modular; planetary stages can be stacked
3 phase brushless motor with a planetary gearbox is a DC planetary gear motor, and it can be mounted directly to AC and DC servo motors. It is widely used in industrial fields of medium precision. Such as printing machine tools, flame-cutting, laser cutting, CNC machine tools, tool machinery, food packaging, automation industry, semiconductor equipment, medical equipment, robots, manipulators, communication equipment, pharmaceutical equipment, printing equipment, packaging machinery, textile machinery, CNC machine tools, CNC pipe bending machine, parking equipment, measuring equipment, work machine, precision monitoring system, vehicle industry, automatic control system and other industries.